Како се обработуваат високопрецизните делови
2023-09-22
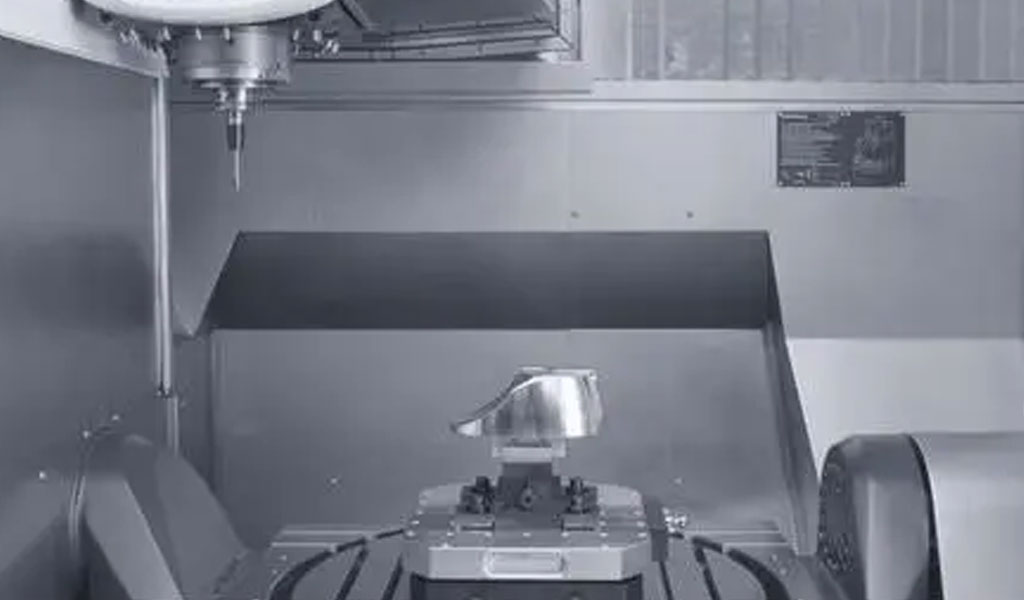
Разбирање на прецизна обработка
Прецизната обработка е камен-темелник на модерното производство, одговорно за производство на сложени и точни компоненти што се користат во широк опсег на индустрии. За целосно да го сфатиме неговото значење, да ги истражиме основните концепти на прецизната обработка, неговата витална улога во различни сектори и историското патување што доведе до нејзината сегашна извонредна состојба.А. Што е прецизна обработка?
Прецизната обработка се однесува на збир на производни процеси кои го отстрануваат материјалот од работното парче со висок степен на точност и контрола, што резултира со фино изработени компоненти со тесни толеранции. Овој процес ги трансформира суровините, како што се металите, пластиката или керамиката, во прецизни делови што ги исполнуваат строгите спецификации. Главните карактеристики на прецизната обработка вклучуваат:- точност: Прецизната обработка осигурува дека финалниот производ точно одговара на планираниот дизајн, со минимално отстапување.
- Тесни толеранции: Овозможува производство на делови со исклучително тесни толеранции, што значи дека готовите компоненти тесно се придржуваат до одредените мерења.
- Супериорна површинска завршница: Прецизната обработка обезбедува исклучителни завршетоци на површината, честопати елиминирајќи ја потребата од дополнителни процеси на завршна обработка.
- Комплексни геометрии: Може да создаде сложени форми, контури и карактеристики, што го прави незаменлив во производството на компоненти со сложени дизајни.
- Повторливост: Прецизност процес на обработкатие се многу повторливи, обезбедувајќи постојан квалитет на повеќе делови.
- разноврсност: Може да се примени на широк спектар на материјали, што го прави погоден за различни индустрии.
B. Важноста на прецизната обработка
Прецизната обработка има огромно значење во неколку критични индустрии, влијаејќи на различни аспекти од нашиот секојдневен живот. Еве неколку убедливи причини за неговата важност:- Воздухопловна индустрија: Во воздушниот сектор, прецизната обработка е неопходна за изработка на компоненти кои издржуваат екстремни услови. Мотори на авиони, слетување опрема, а структурните елементи се потпираат на прецизно обработени делови за безбедност и перформанси.
- Медицински помагала: Медицинските уреди како хируршки инструменти, протетика и имплантирани уреди бараат прецизна обработка за биокомпатибилност, точност и безбедност на пациентот.
- Автомобилски сектор: Прецизно обработените делови се неопходни за автомобилската индустрија за да се обезбеди сигурност и ефикасност на возилата. Компонентите како што се деловите на моторот, системите за пренос и механизмите за сопирање се потпираат на прецизна обработка.
- Електроника и полупроводници: Прецизната обработка е клучна во производството на микроелектронски компоненти и полупроводнички уреди, каде што малите толеранции се императив за функционалност.
- Сектор за енергетика: Енергетската индустрија се потпира на прецизна обработка за производство на критични делови што се користат во производството на електрична енергија, вклучувајќи турбини, генератори и компоненти за пренос.
- Изработка на алатки и матрици: Прецизната обработка е од клучно значење во производството на алати и матрици, кои, пак, се користат за создавање безброј други производи.
- Електроника: Производството на паметни телефони, лаптопи и друга потрошувачка електроника има корист од прецизната обработка за да се обезбеди елегантен дизајн и оптимална функционалност.
- Истражување и развој: Истражувачите и научниците зависат од прецизно обработените компоненти за експерименти, прототипови и лабораториска опрема.
В. Историска перспектива
Патувањето на прецизната машинска обработка се враќа во античките цивилизации, каде што вешти занаетчии користеле рудиментирани алатки за обликување на материјалите. Сепак, прецизноста постигната во тие времиња беше ограничена во споредба со современите стандарди.- Рана прецизна обработка: Индустриската револуција од 18 и 19 век означи клучен период во развојот на прецизната обработка. Пронајдокот на машински алати, како што се стругови и машини за мелење, го револуционизира производството овозможувајќи поголема точност и конзистентност.
- Втората светска војна: Прецизната обработка одигра клучна улога во Втората светска војна, бидејќи беше од суштинско значење за производство на воена опрема со потребната прецизност и униформност. Оваа ера беше сведок на напредокот во техниките на обработка и појавата на нови материјали.
- Повоени напредувања: Повоениот период забележа пораст на технолошките иновации, вклучително и употребата на машини за компјутерска нумеричка контрола (CNC). ЦПУ обработка дозволено автоматизирани и многу прецизни операции, воведувајќи нова ера на производство.
- Дигиталната ера: Интеграцијата на компјутерите и софтверот во процесите на обработка дополнително ја зголеми прецизната обработка. Современите CNC машини можат да извршуваат сложени операции со неспоредлива точност, што ги прави неопходни во денешното производство.
Материјалите и нивното значење
Материјалите се основата на прецизната обработка, а изборот на вистинскиот материјал игра клучна улога во производството на делови со висока прецизност. Во овој дел, ќе истражуваме за важноста на изборот на соодветни материјали, ќе го разбереме значењето на својствата на материјалот и ќе ги истражиме различните фактори кои влијаат на обработливоста.A. Избор на материјали
Изборот на материјали во прецизната обработка е критична одлука која директно влијае на перформансите, издржливоста и функционалноста на финалниот производ. Производителите мора да земат предвид неколку фактори при изборот на материјали:- Соодветност на материјалот: Материјалот мора да биде соодветен за наменетата примена. Различни индустрии и апликации имаат различни барања, како што се отпорност на температура, отпорност на корозија и електрична спроводливост.
- Механички својства: Механичките својства како цврстина на истегнување, цврстина и еластичност се клучни. На пример, во воздушната вселена, материјалите со висока цврстина на истегнување се претпочитаат за структурни компоненти.
- Термички својства: Некои апликации бараат материјали со одлична топлинска спроводливост или отпорност на високи температури. Ова е особено важно во индустриите како што се производството на електрична енергија и електрониката.
- Отпорност на корозија: Во средини каде што корозијата е загрижувачка, се претпочитаат материјали со висока отпорност на корозија, како што се нерѓосувачки челик или титаниум.
- Размислувања за тежината: Индустриите како автомобилската и воздушната често даваат приоритет на лесните материјали како алуминиум или композити од јаглеродни влакна за да ја намалат потрошувачката на гориво и да ги подобрат перформансите.
- Ограничувања на трошоците: Трошоците се значаен фактор во изборот на материјалот. Материјалите со високи перформанси може да бидат скапи, па затоа производителите мора да направат рамнотежа помеѓу перформансите и економичноста.
- Регулаторната усогласеност: Во индустриите како што е здравствената заштита, материјалите мора да исполнуваат строги регулаторни стандарди за биокомпатибилност и безбедност.
- Достапност: Достапноста на материјалите и нивните извори исто така влијаат на изборот. Некои специјализирани легури или композити може да имаат ограничена достапност.
Б. Својства на материјалот
Разбирањето на својствата на материјалите е од клучно значење за прецизната обработка. Еве неколку клучни својства на материјалот и нивното значење:- Затегнувачка цврстина: Јачината на истегнување ја мери способноста на материјалот да издржи сила на влечење без да се скрши. Тоа е од суштинско значење за структурните компоненти и делови подложени на механички стрес.
- Цврстина: Тврдоста ја покажува отпорноста на материјалот на деформација и абење. Цврстите материјали се погодни за алати за сечење, додека помеките материјали може да се претпочитаат за одредени апликации, како заптивки.
- Еластичност: Пластичноста се однесува на способноста на материјалот да се деформира без да се скрши кога е подложен на напрегање на истегнување. Ноктилните материјали полесно се обликуваат, но можеби не се погодни за апликации за кои е потребна ригидност.
- Термичка спроводливост: Материјалите со висока топлинска спроводливост ефикасно ја исфрлаат топлината. Ова својство е од витално значење во апликации каде што контролата на температурата е критична.
- Електрична спроводливост: Електричната спроводливост е од суштинско значење во електрониката и електричните компоненти, каде што материјалите мора да го олеснат протокот на електрична енергија.
- Магнетни својства: Магнетните својства се значајни во индустриите како електромагнетиката и електрониката, каде што материјалите можеби ќе треба да бидат феромагнетни или немагнетни.
- Хемиска отпорност: Материјалите мора да се спротивстават на хемиска корозија во средини каде што се изложени на киселини, бази или други корозивни материи.
В. Фактори на обработливост
Обработливоста се однесува на леснотијата со која материјалот може да се обработува, сече или обликува. Тоа е под влијание на различни фактори, вклучувајќи:- Цврстина на материјалот: Помеките материјали обично се полесни за обработка, додека за поцврстите материјали може да бидат потребни специјализирани алатки и техники.
- Формирање чип: Формирањето и евакуацијата на чипови за време на обработката влијае на ефикасноста на процесот и завршна обработка на површината.
- Носење на алатки: Различни материјали може да предизвикаат различни степени на абење на алатот, што влијае на брзината и цената на обработката.
- Течност за ладење и подмачкување: Правилната течност за ладење и подмачкување се неопходни за намалување на триењето, топлината и абењето на алатот за време на обработката.
- Брзина на сечење: Брзината со која алатот за сечење се движи низ материјалот влијае и на продуктивноста и на квалитетот на обработената површина.
- Материјал за алат: Изборот на материјалот на алатот за сечење, како што е карбид или челик со голема брзина, зависи од материјалот што се обработува.
- Параметри за сечење: Прилагодувањето на параметрите за сечење, како што се стапката на довод и длабочината на сечењето, може да го оптимизира процесот на обработка за одредени материјали.
Машински алати за прецизна обработка
Машинските алати се срцето на прецизната обработка, овозможувајќи трансформација на суровините во делови со висока прецизност. Во овој дел, ќе истражиме четири клучни типови на машински алати кои се користат во прецизната обработка: ЦНЦ машински центри, машини за вртење, машини за брусење и EDM (машина со електрично празнење). Секоја од овие машини игра единствена улога во производството на прецизни компоненти.A. ЦНЦ машински центри
Центрите за обработка на CNC (компјутерска нумеричка контрола) се разновидни и широко се користат во прецизната обработка. Тие се автоматизирани системи кои го контролираат движењето на алатките за сечење и работните парчиња со исклучителна прецизност. Еве преглед на центрите за CNC обработка и нивното значење:- разноврсност: ЦНЦ-центрите за обработка можат да вршат различни операции на обработка, вклучувајќи мелење, дупчење и тапкање. Оваа разновидност овозможува производство на сложени делови со повеќе карактеристики.
- Висока прецизност: Компјутеризираната контрола на CNC машините обезбедува прецизно позиционирање на алатот и конзистентни резултати, што ги прави идеални за делови со тесни толеранции.
- Автоматизација: Центрите за CNC обработка можат да работат континуирано, со минимална човечка интервенција. Оваа автоматизација ја зголемува ефикасноста и го намалува ризикот од грешки.
- Комплексни геометрии: Тие се истакнуваат во обработката на сложени форми и контури, што ги прави погодни за индустрии како што е воздушната, каде сложените компоненти се вообичаени.
- Повторливи резултати: CNC машините нудат одлична повторливост, осигурувајќи дека секој произведен дел одговара на точните спецификации на дизајнот.
- Намалени времиња на поставување: Центрите за обработка на ЦПУ може да се програмираат да се префрлаат помеѓу различни задачи брзо, минимизирајќи го времето на поставување и зголемувајќи ја ефикасноста на производството.
Б. Вртечки машини
Машините за вртење се користат за создавање цилиндрични делови со ротирање на работното парче додека алатката за сечење го отстранува материјалот од неговата надворешна површина. Тие се неопходни за производство вратилоs, иглички и други компоненти со ротациона симетрија. Клучните точки за машините за вртење вклучуваат:- Цилиндрични делови: Машините за вртење се специјализирани за производство на цилиндрични или цевчести компоненти, вклучувајќи ги и оние со навои или сложени жлебови.
- Големи брзини: Тие работат со големи брзини, што ги прави погодни за делови кои бараат мазна и прецизна завршница.
- Операција со една оска: Повеќето машини за вртење се со една оска, фокусирајќи се на обликувањето на надворешната површина на работното парче.
- Ефикасно за масовно производство: Вртењето е високо ефикасно за масовно производство на делови со минимален материјален отпад.
- Машини за струг: Машините за струг со рачни и CNC контролирани се најчесто користени машини за вртење, кои нудат голем број на способности.
В. Машини за брусење
Машините за брусење се дизајнирани за прецизно завршување на површината и обликување на тврди или абразивни материјали. Тие се клучни за постигнување екстремно тесни толеранции и врвни завршетоци на површината. Еве зошто машините за мелење се значајни:- Прецизност на микрониво: Машините за брусење можат да постигнат прецизност на ниво на микрони, што ги прави неопходни за апликации кои бараат највисоко ниво на точност.
- Отстранување материјал: Тие го отстрануваат материјалот со абразија, овозможувајќи корекција на несовршеностите на површината и постигнување исклучителна мазност.
- Мелење со алат и секач: Покрај површинското брусење, постојат специјализирани машини за брусење за острење на алати за сечење и производство на прецизни профили.
- Разновидност на методи за мелење: Различни типови машини за мелење, вклучително и површински брусилки, цилиндрични брусилки и брусилки без центар, задоволуваат различни потреби за обработка.
- Стврднати материјали: Мелењето е особено погодно за стврднати материјали како челик за алат и керамика, каде што традиционалните методи на обработка може да бидат неефикасни.
D. EDM (машина со електрично празнење)
EDM, или обработка со електрично празнење, е нетрадиционален процес на обработка што користи електрични празнења за обликување на материјалите. Идеален е за создавање сложени и нежни делови каде традиционалните алатки за сечење можат да предизвикаат оштетување. Клучните аспекти на EDM вклучуваат:- Нема физички контакт: EDM не вклучува директен физички контакт помеѓу алатот и работното парче, минимизирајќи го ризикот од абење на алатот и оштетување на кревки материјали.
- Висока прецизност: Може да постигне висока прецизност и квалитет на завршна површина, дури и со исклучително тврди материјали.
- Жица EDM и Sinker EDM: Постојат два основни типа на EDM машини: сечење на жица EDM, кој користи жичана електрода и мијалник EDM, кој користи обликувана електрода.
- Комплексни форми: EDM може да произведе сложени форми, како што се матрици и калапи, со сложени детали и фини карактеристики.
- Зона погодена од топлина: Бидејќи EDM не генерира топлина на работното парче, тој е погоден за материјали чувствителни на топлина како што се воздушните легури.
- Бавен процес: EDM е релативно бавен во споредба со другите методи на обработка, што го прави најдобро прилагоден за работи со мала количина и висока прецизност.
Алатки за сечење и алати
Алатите за сечење се во првите редови на прецизната обработка, служејќи како инструменти кои ги обликуваат и трансформираат суровините во делови со висока прецизност. Во овој дел, ќе ги истражиме различните видови алатки за сечење, важноста на облогите на алатот и факторите кои влијаат на животниот век и абењето на алатот.A. Видови алатки за сечење
Прецизната обработка се потпира на разновидна палета на алатки за сечење, секој дизајниран за специфични задачи и материјали. Изборот на алат за сечење во голема мера влијае на ефикасноста и точноста на процесот на обработка. Еве неколку вообичаени видови алатки за сечење:- Енд Милс: Крајните мелници се разновидни алатки кои се користат за операции на мелење. Тие имаат повеќекратни рабови за сечење и можат да го отстранат материјалот од работното парче на различни начини, вклучително свртување, контура и процепи.
- Вежби: Дупчалките се дизајнирани за создавање дупки во работните парчиња. Тие доаѓаат во различни форми, вклучувајќи дупчалки за вртење, централни дупчалки и вежби со индексирање.
- Вртење влошки: Се користат во машините за вртење за обликување на цилиндрични делови. Влошките за вртење се достапни во различни форми и материјали за да одговараат на различни апликации.
- Фрези: Фрезите доаѓаат во различни форми, како што се мелници за лице, топчести мелници и секачи со жлебови, и се користат во машините за мелење за да се создадат различни карактеристики на работното парче.
- Ризерс: Завртките се користат за доработка и димензионирање на претходно дупчените дупки до прецизни димензии. Тие обезбедуваат мазни и точни површини со дупки.
- Допрете и умира: Овие алатки за сечење се користат за операции на навој. Допрете создаваат внатрешни нишки, додека матриците создаваат надворешни нишки.
- Тркала за мелење: Тркалата за брусење се абразивни алатки кои се користат за прецизно мелење на површината. Достапни се во различни абразивни материјали и големини на ронки.
- Брошеви: Бришевите се специјализирани алатки кои се користат за сечење внатрешни и надворешни облици и профили, како што се клучеви и шилки.
- Контрабури и контраминици: Овие алатки се користат за создавање на вдлабнатини или гребени околу дупки за споитеs.
- Досадни барови: Досадните шипки се користат во здодевните операции за прецизно зголемување на постоечките дупки.
Б. Облоги за алат
Облогите за алат се тенки слоеви на материјал кои се нанесуваат на алати за сечење за да се подобрат нивните перформанси и издржливост. Овие облоги имаат неколку предности:- Намалено триење: Облогите како титаниум нитрид (TiN) и титаниум карбонитрид (TiCN) го намалуваат триењето помеѓу алатот и работното парче, што доведува до помазно сечење и подолг век на траење на алатот.
- Зголемена цврстина: Облогите ја зголемуваат тврдоста на површината на алатот, што ја прави поотпорна на абење и го продолжува животниот век на алатот.
- Подобрена отпорност на топлина: Облогите можат да издржат високи температури генерирани за време на обработката, намалувајќи го абењето на алатот поврзано со топлина и зголемувајќи ја брзината на сечење.
- Својства против градење: Некои премази имаат својства против адхезија, спречувајќи наталожување на материјал на сечечките рабови на алатот.
- Зголемено подмачкување: Обложените алатки имаат подобрено подмачкување, намалувајќи ја потребата од прекумерна течност за ладење и ја подобруваат евакуацијата на чиповите.
В. Животот и носењето на алатките
Разбирањето на животниот век и абењето на алатот е од клучно значење за оптимизирање на процесите на обработка и минимизирање на трошоците за производство. Времетраењето на алатот се однесува на времетраењето додека алатката за сечење останува ефективна пред да бара замена или реконструкција. Неколку фактори влијаат на животниот век и абењето на алатот:- Брзина на сечење: Поголемите брзини на сечење може да доведат до зголемено абење на алатот поради повисоките температури генерирани за време на обработката. Правилниот избор на брзини на сечење е од суштинско значење за да се балансира животниот век на алатот и продуктивноста.
- Стапка на храна: Брзината со која алатот за сечење напредува во работното парче влијае на абењето на алатот. Високите стапки на довод може да го забрзаат абењето, додека пониските стапки на довод може да го продолжат животниот век на алатот.
- Длабочина на сече: Длабочината на сечењето влијае на количината на отстранетиот материјал по поминување. Подлабоките сечи може да го зголемат абењето на алатот, така што оптимизирањето на длабочината е критично.
- Цврстина на материјалот: Сечењето тврди материјали може да го забрза абењето на алатот. Специјализирани алатки и премази се користат за ефикасно обработување на тврди материјали.
- Течност за ладење и подмачкување: Правилната течност за ладење и подмачкување помагаат да се троши топлината и да се намали триењето, со што се продолжува животниот век на алатот.
- Материјал за алат: Материјалот од кој е направен алатот за сечење влијае на неговата отпорност на абење. Материјалите како карбид и керамика нудат одлична отпорност на абење.
- Геометрија на алатки: Геометријата на алатот за сечење, вклучувајќи го аголот на гребло, аголот на олеснување и дизајнот на кршачот на чипови, игра значајна улога во моделите на абење.
- Материјал за работното парче: Типот на материјалот што се обработува влијае на абењето на алатот. Абразивните материјали може да доведат до побрзо абење на алатот.
Процеси на прецизна обработка
Процесите на прецизна обработка се методи со кои суровините се трансформираат во делови со висока прецизност со тесни толеранции и исклучителни завршетоци на површината. Во овој дел, ќе истражиме пет клучни процеси на прецизна обработка: вртење, глодање, дупчење, мелење и обработка со електрично празнење (EDM). Секој од овие процеси служи за единствена цел и се користи врз основа на специфичните барања на работното парче.A. Вртење
Вртењето е процес на обработка што првенствено се користи за обликување на цилиндрични делови. Тоа вклучува ротирање на работното парче додека алатката за сечење со една точка го отстранува материјалот од надворешната површина. Еве ги клучните аспекти на вртењето:- Цилиндрични делови: Вртењето е идеално за производство на цилиндрични компоненти како што се вратила, иглички и чаури.
- Ротациона симетрија: Добро е прилагоден за делови за кои е потребна ротациона симетрија, бидејќи работното парче се ротира на струг додека алатот за сечење го обликува.
- Различни операции: Вртењето може да врши различни операции, вклучувајќи свртување, вртење (намалување на дијаметарот), заострено вртење и навој.
- Сечење со една точка: Една алатка за сечење го отстранува материјалот со континуирано движење, што резултира со ефикасно отстранување на материјалот.
- Машини за струг: За операции на вртење вообичаено се користат и рачни и CNC-контролирани машини за струг.
Б. Мелење
Мелењето е разновиден процес на прецизна обработка што користи алатки за сечење со повеќе точки за отстранување на материјалот од работното парче. Тој е добро прилагоден за создавање широк спектар на форми и карактеристики. Главните аспекти на мелењето вклучуваат:- разноврсност: Мелењето може да произведе рамни површини, слотови, џебови и сложени контури. Се користи и за 2D и за 3D обработка.
- Сечење со повеќе точки: Повеќекратните рабови за сечење на алатот се во интеракција со работното парче истовремено, овозможувајќи ефикасно отстранување на материјалот.
- Видови мелење: Мелењето може да се изведе со користење на различни типови секачи, вклучувајќи крајни мелници, мелници за лице и топчести мелници.
- Центри за обработка на ЦПУ: Машините за мелење контролирани со CNC нудат прецизна контрола врз движењето на алатот и широко се користат во модерната обработка.
- Големи брзини: Мелењето може да се врши со големи брзини, што овозможува ефикасно производство.
В. Дупчење
Дупчењето е процес на прецизна обработка што се користи за создавање дупки во работните парчиња. Тоа е основна операција во различни индустрии. Главните аспекти на дупчењето вклучуваат:- Создавање дупка: Машините за дупчење користат специјализирани алатки наречени дупчалки за отстранување на материјалот и создавање дупки со специфични дијаметри.
- Видови дупчалки: Достапни се различни типови на дупчалки, вклучувајќи дупчалки за вртење, централни дупчалки и дупчалки со индексирање, секоја дизајнирана за специфични апликации.
- точност: Прецизното позиционирање и усогласување се од суштинско значење при дупчењето за да се осигура дека дупките се создаваат со точност.
- Брзина и стапка на напојување: Параметрите за дупчење како што се брзината на вртење и брзината на довод се клучни за постигнување на саканите димензии на дупката.
- Течност за ладење и подмачкување: Соодветното средство за ладење и подмачкување се користат за да се исфрли топлината и да се намали триењето за време на дупчењето.
Д. Мелење
Брусењето е прецизен процес на обработка што користи абразивни тркала за отстранување на материјалот и постигнување на екстремно тесни толеранции и завршни површини. Клучните аспекти на мелење вклучуваат:- Исклучителна прецизност: Мелењето може да постигне прецизност на ниво на микрони, што го прави идеален за апликации за кои е потребна најголема точност.
- завршна површина: Произведува супериорни завршетоци на површината, честопати елиминирајќи ја потребата од дополнителни процеси на завршна обработка.
- материјали: Мелењето е погодно за тврди и абразивни материјали, вклучувајќи стврднат челик, керамика и карбиди.
- Разновидност на методи за мелење.
- Течноста за ладење: Правилното средство за ладење е од суштинско значење при мелењето за да се спречи прегревање и да се одржи интегритетот на тркалата.
Д. Обработка со електрично празнење (EDM)
EDM, или обработка со електрично празнење, е нетрадиционален процес на прецизна обработка што користи електрични празнења за отстранување на материјалот. Тој е особено погоден за обработка на сложени и сложени форми, како и за тврди и отпорни на топлина материјали. Клучните аспекти на EDM вклучуваат:- Бесконтактна обработка: EDM не вклучува директен контакт помеѓу алатот и работното парче, со што се намалува ризикот од абење и оштетување на алатот.
- Висока прецизност: EDM може да постигне висока прецизност, што го прави погоден за апликации каде што се неопходни тесни толеранции.
- Комплексни форми: Се истакнува во обработката на сложени форми, матрици, калапи и компоненти со фини детали.
- Жица EDM и Sinker EDM: Постојат два примарни типа на EDM машини: жичен EDM, кој користи жичана електрода, и Sinker EDM, кој користи обликувана електрода.
- Бавен процес: EDM е релативно бавен во споредба со другите методи на обработка, што го прави најдобро прилагоден за работи со мала количина и висока прецизност.
Толеранции и контрола на квалитет
Прецизната обработка бара прецизно внимание на деталите и ригорозна посветеност на контролата на квалитетот за да се осигура дека деловите ги исполнуваат наведените стандарди. Во овој дел, ќе истражиме три критични аспекти на контролата на квалитетот во прецизната обработка: геометриско димензионирање и толеранција (GD&T), статистичка контрола на процесите (SPC) и обезбедување на квалитет.А. Геометриско димензионирање и толеранција (GD&T)
Геометриското димензионирање и толеранција, честопати скратено како GD&T, е систем кој се користи за дефинирање и пренесување на дозволените варијации во големината, формата, ориентацијата и локацијата на карактеристиките на делот. GD&T е од витално значење во прецизната обработка од следниве причини:- Прецизна комуникација: GD&T обезбедува стандардизиран јазик за инженерите, дизајнерите и машинистите за прецизно да ги соопштат намерите на дизајнот и барањата за димензии.
- Појаснување за толеранција: Помага да се дефинира прифатливата варијација во критичните димензии, осигурувајќи дека сите засегнати страни ги разбираат дозволените отстапувања.
- Подобрен квалитет: GD&T промовира подобрен квалитет со намалување на двосмисленоста во дизајнерските спецификации, минимизирајќи го ризикот од грешки при обработката.
- Ефикасност на трошоците: Јасните спецификации на GD&T може да доведат до намалени трошоци за производство, бидејќи е помала веројатноста дека деловите ќе бидат укинати или ќе бараат преработка поради недоразбирање или погрешно толкување.
- Комплексна геометрија: Особено е корисен за делови со сложени геометрии, осигурувајќи дека сите карактеристики се произведени според саканите спецификации.
Б. Статистичка контрола на процесите (СПЦ)
Статистичката контрола на процесите (SPC) е методологија за контрола на квалитетот која користи статистички техники за следење и контрола на процесот на обработка. SPC е од суштинско значење во прецизната обработка од следниве причини:- Мониторинг на процеси: SPC помага да се следат процесите на обработка во реално време, идентификувајќи варијации или отстапувања од саканите параметри.
- Рано откривање на проблеми: Со континуирано следење на процесот, SPC овозможува рано откривање на проблеми кои би можеле да доведат до делови надвор од спецификациите, намалување на отпадот и преработка.
- Донесување одлуки засновани на податоци: SPC се потпира на податоци и статистичка анализа за да донесува информирани одлуки за прилагодувањата на процесот, осигурувајќи дека процесот на обработка останува во прифатливи граници.
- Подобрена конзистентност: SPC промовира конзистентност на процесот и ја намалува веројатноста за производство на несоодветни делови.
- Намален отпад и преработка: Со навремено идентификување и адресирање на варијациите на процесот, SPC го минимизира производството на неисправни делови, намалувајќи ги трошоците за отпадоци и преработка.
В. Обезбедување квалитет во прецизната обработка
Обезбедувањето квалитет во прецизната обработка опфаќа сеопфатен пристап за да се осигура дека произведените делови ги исполнуваат или надминуваат одредените стандарди за квалитет. Тоа вклучува различни елементи, вклучувајќи:- Процесна документација: Деталната документација на процесите на обработка, вклучувајќи ги стандардните работни процедури (СОП) и упатствата за работа, гарантира дека секој чекор се изведува доследно.
- Инспекција и мерење: Ригорозната инспекција и мерење со помош на прецизни инструменти и метролошки техники потврдуваат дека деловите се усогласени со специфицираните толеранции и стандарди за квалитет.
- Калибрација: Редовната калибрација на машинската опрема и мерните инструменти е од суштинско значење за одржување на точноста и следливоста.
- Проверка на материјалот: Потврдувањето на својствата, составот и квалитетот на материјалот е од клучно значење за да се осигура дека употребениот материјал ги исполнува дизајнерските барања.
- Обука за вработените: Програмите за обука и развој на вештини за машинистите и персоналот за контрола на квалитетот гарантираат дека тие се умешни во нивните улоги и одговорности.
- Анализа на коренити причини: Кога се идентификуваат несоодветните делови, се спроведува анализа на основната причина за да се утврди изворот на проблемот и да се спроведат корективни активности.
- Континуирано подобрување: Културата на постојано подобрување поттикнува иновации и поттикнува тековни подобрувања во процесите на обработка и процедурите за контрола на квалитетот.
- Клиент коментари: Собирањето и анализата на повратните информации од клиентите помага да се идентификуваат областите за подобрување и да се усогласат процесите на обработка со очекувањата на клиентите.
Заклучок
А. Уметноста и науката за прецизна обработка
Прецизната обработка стои на пресекот на уметноста и науката, каде што креативноста, вештината и иновативноста се спојуваат за да произведат високопрецизни делови што ги поттикнуваат индустриите и го обликуваат модерниот свет. Тоа е и уметничка форма, која бара изработка и експертиза на машинистите кои ги трансформираат суровините во дела со инженерска извонредност, и наука која се потпира на врвна технологија, наука за материјалите и напредни процеси за да постигне неспоредлива прецизност. Патувањето на прецизната обработка нè води низ разбирањето на материјалите и нивните својства, мајсторството на алатките и машините за сечење и прецизната контрола на процесите и толеранциите. Го опфаќа јазикот на геометриското димензионирање и толеранција, будноста на статистичката процесна контрола и посветеноста на обезбедувањето квалитет. Прецизната обработка игра клучна улога во различни индустрии, од воздушната и автомобилската индустрија до медицинските уреди и електрониката, обликувајќи сè, од авионски мотори до вештачки зглобови и микрочипови. Овозможува создавање на компоненти кои работат со неспоредлива точност и сигурност, често поместувајќи ги границите на она што е можно.Б. Завршни мисли
Како што го заклучуваме ова истражување на прецизната обработка, јасно е дека ова поле не е само за создавање на делови; се работи за создавање на можности. Потрагата по прецизност поттикнува иновации, поместувајќи ги границите на она што може да се постигне. Без разлика дали се работи за деликатната изработка потребна за создавање на сложени запчаници на часовникот или за напредната технологија потребна за производство на сложени воздушни компоненти, прецизната обработка е во срцето на сето тоа. Иднината на прецизната обработка е исполнета со ветувања. Напредокот во науката за материјали, автоматизацијата и дигиталните технологии продолжуваат да го преобликуваат пејзажот. Минијатуризацијата, 3D печатењето и практиките на одржливо производство стануваат сè поистакнати, отворајќи нови хоризонти за индустријата. Во свет каде што прецизноста е важна повеќе од кога било, прецизната обработка останува незаменлив столб на модерното инженерство. Тоа е доказ за човечката генијалност и нашиот непопустлив стремеж за извонредност во секој аспект на производството. Како што расте побарувачката за поголема прецизност и покомплексни компоненти, прецизната обработка ќе продолжи да се развива, одговарајќи на предизвиците на утре со истата посветеност и прецизност што ја дефинирале со векови.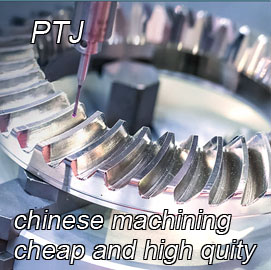
Нашите услуги
- Обработка на 5 оски
- Cnc мелење
- Свртување на ЦНЦ
- Обработка на индустрии
- Процес на машинска обработка
- Површински третман
- Обработка на метали
- Обработка на пластика
- Калап за металургија во прав
- Умирање
- Галерија на делови
Студии на случај
- Авто метални делови
- Машински делови
- LED ладилник
- Градежни делови
- Мобилни делови
- Медицински делови
- Електронски делови
- Прилагодена обработка
- Делови за велосипеди
Список на материјали
- Обработка на алуминиум
- Обработка на титаниум
- Обработка од нерѓосувачки челик
- Обработка на бакар
- Месинг обработка
- Обработка на супер легури
- Ekиркаат машинска обработка
- Обработка на UHMW
- Еднострана обработка
- PA6 Обработка
- Обработка на ППС
- Тефлонска обработка
- Инконел Обработка
- Обработка на челични алатки
- Повеќе материјал
Галерија на делови